Troubleshooting gear pump assisted single-screw extrusion pr
Troubleshooting gear pump assisted single-screw extrusion processes:
Gear pumps are often used in tandem with single-screw extruders to increase rate, decrease resin consumption, improve process stability, and decrease the extrude temperature.
When a process is unstable, it is often not obvious if the extruder is unstable and the gear pump is operating well, or the extruder is operating well and the gear pump operation is unstable. This paper will describe a few operations where gear pumps improved a process, how they can be used in unstable processes, and approaches to troubleshooting lines using gear pumps.
Troubleshooting gear pump assisted single-screw extrusion processes Introduction:
Gear pumps are often positioned between smooth-bore single-screw extruders and dies, providing several processing advantages. These advantages include the mitigation of pressure surges and thus flow surges from the extruder, a decrease in the discharge temperature by generating part of the pressure required for the die by the pump instead of by the extruder, reducing resin consumption, and for rate increases. For example, if the extruder is operating with a relatively small pressure oscillation with time (or pressure surge) to the inlet of a gear pump, the gear pump will provide a nearly constant outlet pressure and flow rate to the downstream equipment such as a die. Stable operations with a gear pump will allow plant personnel to operate at the lower specification limits for sheet or film and thus reduce the resin consumption per unit of product. If a gear pump is contributing to the generation of the discharge pressure for the downstream equipment, the metering section will operate with a higher specific rate as compared to a process without a pump. Extruders that operate at a higher specific rate will generally operate at a lower discharge temperature. A gear pump used with a two-stage, vented screw can allow high operating rates at higher discharge pressures while not causing material to flow into the vent.
For gear pump assisted extrusion, the extruder control algorithms are set to maintain a constant pressure to the inlet side of the pump by the extruder. The pump is operated at a constant rotational speed and thus it delivers molten polymer at a very steady and controlled rate. A schematic of a gear pump assisted extrusion process is shown in Figure 1 for a single-stage extruder. If the pressure to the inlet of the pump is less than the set point value, then the control algorithm will increase the screw speed of the extruder. Conversely, if the inlet pressure is too high the control system will decrease the screw speed.
For properly designed systems, the screw speed will only have relatively small changes to compensate for slight changes in the pump inlet pressure. But for extrusion processes that are not operating properly and show severe flow surging, the screw speed will have large variations.
Diagram of a typical gear pump installation for a single-stage extruder and a screen filtering system. The control schematic for extruder screw speed is included.
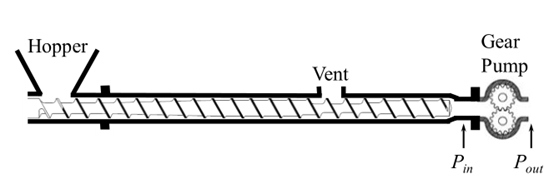
Gear pumps allow higher rates and higher discharge pressures for two-stage, vented extruders. A schematic of this process is shown in Figure 2. Since the vent is at atmospheric pressure or under vacuum, all pressure required to operate the die for a system without a gear pump must be generated in the second-stage metering section of the screw. If the pressure required to operate the die is higher than what the second stage metering channel can develop, then molten resin will flow into the vent opening. A gear pump, however, can allow higher rates and higher discharge pressures while eliminating vent flow. For this case, the metering section only needs to generate enough pressure to operate safely the pump, a pressure typically about 2 to 8 MPa. This pressure level is high enough to keep the gear channels completely full of resin and maintain lubrication in the bearings. The pump will then increase the pressure to a higher level as required by the downstream equipment. Moreover, if the gear pump is generating most of the pressure required for the downstream equipment, then the screw and extrusion process can be optimized to a lower discharge temperature.
The goal of this paper is to show the attributes of positioning a gear pump in tandem with a single-screw extruder, and provide troubleshooting methods for tandem operation.
pre:
Melt pumps for blown film extrusion
next:
Improperly designed metering section for a two-stage screw
Inquiry
Please feel free to give your inquiry in the form below. we will reply you quickly!